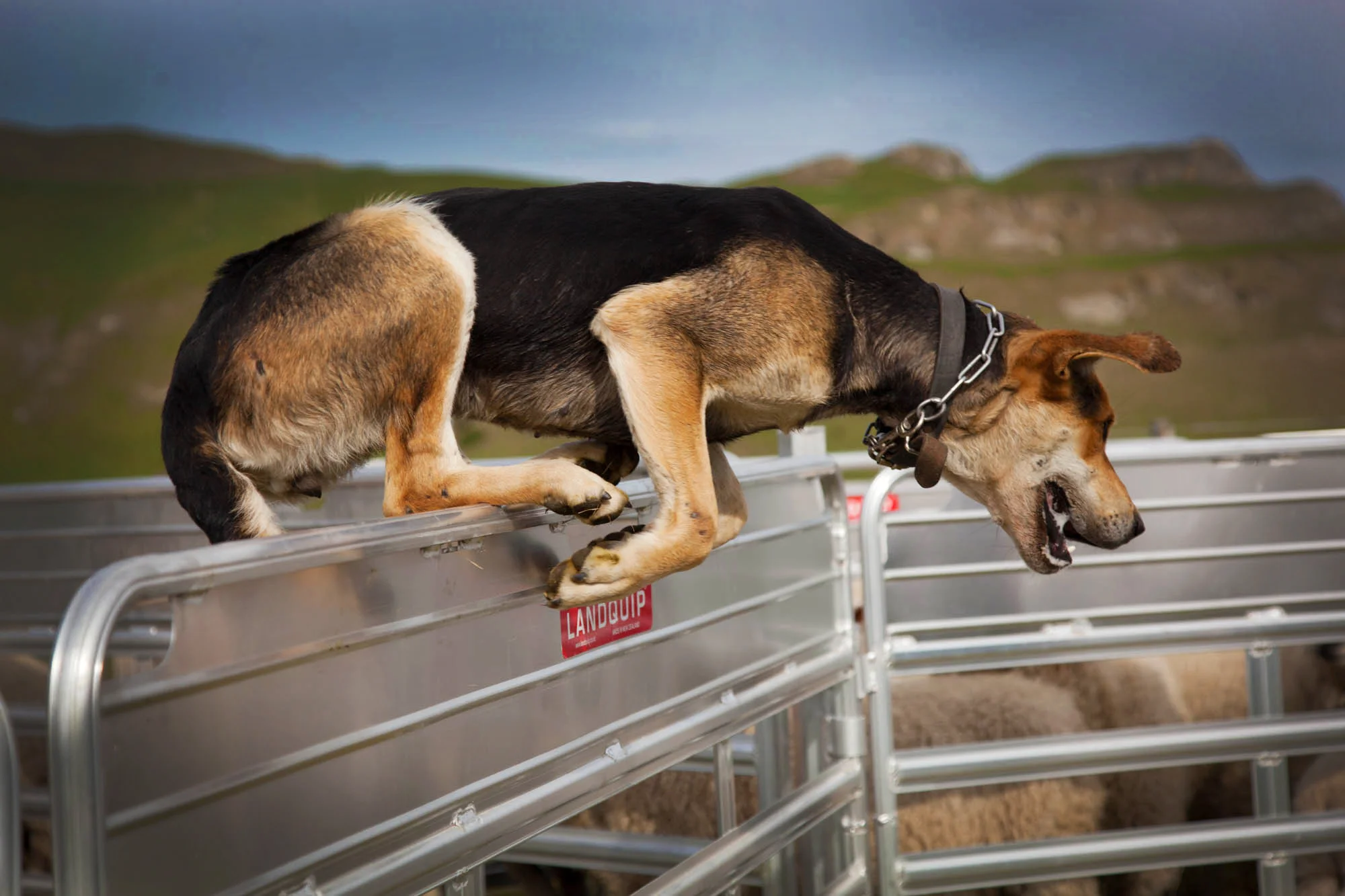
What’s Going on at Wise Ag?
£22 million awarded to farmers to boost productivity
More than 3,600 farmers receive money to spend on time-saving and innovative farm equipment. RPA Chief Executive Paul Caldwell is encouraging customers to contact suppliers early to ensure items can be delivered ahead of claim deadline. Wise Agriculture Ltd is offering nationwide delivery on cattle handling equipment.
More than 3,600 farmers are set to benefit from £22 million in productivity-boosting equipment from round two of the government’s Countryside Productivity Small Grants scheme.
Under the scheme, farmers can apply for grants of between £3,000 and £12,000 to invest in new and innovative equipment – from livestock monitoring cameras to precision farming technology – which help businesses save time and money and improve productivity.
Arrowquip’s Q-Catch 86 Series Cattle Crush features a full-length dual parallel squeeze. With poly bushings on all pivot and latch points and a floor made from virgin Goodyear tractor tyre grade rubber, the 86 Series is world renowned for quiet livestock handling. The Q-Catch 86 Series Cattle Crush is available for nationwide delivery from Wise Agriculture Ltd.
Farming Minister George Eustice confirmed today that all eligible applications have been approved as part of round two of the successful scheme, with the Rural Payments Agency writing to the 3,677 successful applicants from today.
The first round of funding opened in 2018, with £15 million spent to support farmers investing in technology to boost their productivity. Today’s announcement means that £37 million has been allocated to farmers in the scheme’s first two funding rounds, with a third and final funding round to open in autumn 2020.
Farming Minister George Eustice said:
Boosting farm productivity is hugely important, and I’m delighted we’ve been able to fund all applications, supporting farmers to invest in game-changing technology.
As a former farmer I know that new equipment can provide a real boost, saving businesses time and money while improving yields
When we introduce our landmark Agriculture Bill we will set out further measures to help farmers become more productive, efficient and resilient.
Wise Agriculture Ltd can help provide full system designs, taking into account other equipment and space restrictions for individual farms. Arrowquip’s full system handling systems utilise animal behaviour research with functional design to improve the efficiency of day-to-day cattle handling.
The Rural Payments Agency is encouraging farmers to speak to their suppliers to confirm the items they wish to order are available before accepting their grant by using the acceptance portal on GOV.UK by 10 November.
New items were added to the list of the equipment available for the second round of the Small Grants Scheme, with grants available to minimise soil compaction in fields, monitor ammonia levels in farm buildings, and increase machinery precision when applying slurry.
Farmers are encouraged to make early orders to leave time for deliveries to arrive and payment claims to be processed by the end of May 2020.
Rural Payments Agency Chief Executive Paul Caldwell said:
The Small Grants scheme is extremely popular with farmers, so it is fantastic to see the funding is being made available for all the eligible applications we received for round two. Harnessing innovative technology can provide a real boost for productivity across the farming sector in England, and I am delighted that we are able to help unlock access to new equipment for many farmers.
I would encourage all our customers to contact their suppliers early to ensure their items can be delivered ahead of the claim deadline.
More information on the Countryside Productivity Small Grants scheme can be found here.
Increasing the effectiveness of modified live vaccines
Vaccines, in general, are a great tool for preparing calves to respond to a disease challenge. However, developing a sound immune foundation in calves requires multiple tools working together. This guide will address the handling and administration of vaccine.
By Manny Encinias, John Wenzel
College of Agricultural, Consumer and Environmental Sciences, New Mexico State University
Vaccines, in general, are a great tool for preparing calves to respond to a disease challenge. However, developing a sound immune foundation in calves requires multiple tools working together. The most common reasons why vaccinated calves still get sick or fail to fully respond include, but are not limited to nutritional imbalances, age, stress level, genetics, improper vaccine type, improper timing or route of administration, and/or improper handling of vaccine. This guide will address the handling and administration of vaccine.
The Q-Catch 86 Series Manual Squeeze Crush has multiple access points to allow for safe and proper injections.
In most weaning vaccination schedules, modified live vaccines (MLVs) have become an industry-recommended standard to help build immunity against viral bovine respiratory disease (BRD) pathogens. The use of MLVs, rather than killed vaccines, in weaning vaccination programs for calves is typically recommended because MLVs (1) provide a longer and more comprehensive immune response, (2) are administered in a smaller dose, and (3) are typically less expensive.
While MLVs provide the most bang for the buck, it is important to take note of strategies to increase their effectiveness in your weaning vaccination schedule. Rest assured, companies producing and distributing MLVs have done their homework (and checked it) to ensure their products, when handled and administered properly, will achieve a desirable and realistic level of effectiveness. The live viruses commonly used to build broad spectrum immunity against BRD require a minimum number of each virus to replicate and stimulate the immune system. However, because these live viruses are susceptible to damaging effects of excessive heat, ultraviolet (UV) light, and disinfectants, improper handling could kill enough viral particles within a bottle of MLV that a single dose would no longer contain a sufficient number of live viruses to properly immunize the animal. The following are a list of items to consider and review before you purchase and use MLVs at weaning.
Select high-quality products
Do not settle for what is available in the cooler. Do some product searching and look for credible research comparisons between commercially available MLVs. Consult a local veterinarian, followed by university Extension specialists, to help you reason through product data objectively.
Read product labels
Companies spend big dollars on label development. The label will provide essential information regarding vaccine type, dosage, injection method, storage temperature, and expiration date. Don't take a chance with expired products.
Refrigerate and keep cool
All vaccines must be kept cool. When buying vaccines at a local establishment or via mail order, ensure they are cool at the time of purchase or arrival. Maintain the vaccines in a cool environment on the drive back to the ranch. Keep vaccines refrigerated until use. At processing, ensure all vaccine (mixed and unmixed) stays cool until the vaccine is administered. Store multi-dose syringes with vaccines in a closed, portable cooler at chute-side. Do not freeze vaccines as freezing will destroy them.
Protect from sunlight
Never allow vaccines to sit in direct sunlight (e.g., on dashboard, seat, tailgate, working table). Since most operations in the Southwest do not have covered facilities to process calves at weaning, storing vaccines in a cooler with ice packs is the most desirable means to handle vaccines. Use caution and do not lay the multidose syringe in the sunlight between calves, as UV light will kill MLV vaccines.
Mix properly and only what can be used in thirty minutes
Mix MLVs according to label recommendations. Using a transfer needle is an inexpensive means to minimize contamination. Once the diluent and freeze-dried MLV fraction are combined, do not shake vigorously into solution; instead, swirl gently until all freeze-dried fraction has completely dissolved. Furthermore, mix only enough MLV to be administered in 30 minutes. Even properly handled MLVs will begin to lose effectiveness shortly after being mixed.
Administer the MLV product properly
Follow the label guidelines for proper route and timing of administration. It is of the utmost importance that MLV vaccines be administered correctly. Use the proper route—(intramuscular) IM or subcutaneous (Sub-Q)—and the recommended needle gauge and length. Change needles frequently and always follow proper beef quality assurance guidelines when any product is administered to cattle.
Use quality assurance guidelines for syringes and needles
Consider using multi-dose rather than continuous fill syringes when administering vaccines at weaning because multi-dose syringes can be easily stored in a cooler. To minimize contamination, never draw vaccine out of a working bottle (bottle with mixed vaccine) with a used needle. Appropriately label and check calibration of syringes to avoid mixing different types of vaccines and to ensure adequate doses are being administered. After each use, only use boiling water to disinfect syringes. Do not sterilize syringes with chemical disinfectants (e.g., soap, bleach, nolvasan, alcohol, betadine) as they will kill the viral particles in MLVs.
In closing, remember that the effectiveness of a herd health program will only be as strong as the relationship between a ranch manager and a cooperating veterinarian. Regular consultation with a cooperating veterinarian is the key to adapting a herd health program to fit your operation.
This article was published with education permissions by New Mexico State University. Click here for the original post.
Understanding low-stress cattle handling
American guest contributors from Michigan State University outline the fundamentals to low-stress cattle handling and how it can benefit beef and dairy producers.
By guest contributors Ben Bartlett, Michigan State University Extension Educator and Janice Swanson, Michigan State University Animal Science Professor
The advantages of low-stress cattle handling include increased profit for dairy and beef producers. Low-stress cattle handling is easier and safer for people, induces less cattle stress and injury, and produces a better product with a better public image. The best news is that it’s free—well, almost free. The only cost of low-stress cattle handling (LSCH) is the time it takes to learn about cattle and then practice the necessary skills. It is that simple.
Arrowquip’s BudFlow Tub uses animal behaviour to enhance cattle flow. Cattle enter at the front of the tub, once the gate is closed and the operator moves to the rear of the tub, the cattle naturally want to turn back and face the exit.
Low-stress cattle handling
The secret to LSCH is understanding why cattle act the way they do and then using that knowledge to “ask” and not force them to do what you want. We also want our facilities to help us do our work better and not be a barrier. However, even well-designed facilities will not make up for poor handling skills and a lack of cattle behaviour knowledge.
Why do cattle act like cattle?
Arrowquip’s Q-Catch 86 Series Manual Squeeze Crush is world renowned for quietness. Rubber bushings prevent any metal on metal clanging.
Three ingredients control an animal’s actions: anatomy, instinct and experience. Let’s look at anatomy first. Cattle see the world differently than we do. Because they are prey animals, their eyes are shaped differently and are located on the sides of their heads. A cow can see up to 300 degrees around itself, whereas a human has roughly a 140-degree field of vision. Cow eyes are more rectangular—our eyes are round—and have silted rather than round pupils. They see most things with only one eye and therefore don’t have good depth perception. Cattle cannot see directly behind them and worry when people are in their blind spot. Cattle also have limited vertical vision and have to put their heads down to see the ground in front of them. Their vision limitations mean that a shadow across an alley will stop them in their tracks, or a quick motion detected out of the corner of one eye will send them running. When they are a safe distance away, they will turn and face the disturbance so they can get a better look with both eyes. Cattle can see a lot but don’t see it well. Cattle do have keen hearing, and any loud noise—especially angry people’s voices—is very disturbing. In fact, research has demonstrated that people yelling can be more stressful than even the use of a hot shot. However, cattle have difficulty pinpointing where the sound came from. All loud noises will frighten animals, even if we understand that the noise should not be an issue. Cattle have a sensitive sense of smell, though they rely more on vision. Instincts are those things that we all do because we are hard-wired to do them. We jump or startle at loud noises, for example. Cattle are prey animals and find safety in numbers. An isolated or single animal becomes distressed just because it is by itself. Cattle will take their time to slowly explore anything new in their environment.
Cattle do have keen hearing, and any loud noise—especially angry people’s voices—is very disturbing. In fact, research has demonstrated that people yelling can be more stressful than even the use of a hot shot. However, cattle have difficulty pinpointing where the sound came from.
The coat flapping on the side of the chute is a BIG deal to them and is translated to mean danger. When cattle move, they like to follow one another, partly because they then don’t need to look where they are going (remember, they cannot see their feet without putting their heads down) and partly because they are staying with the group. Other behavioural characteristics include a preference to move toward areas with better lighting and uphill instead of downhill. Experience rounds out why cattle act the way they do. They can quickly learn that a tractor and wagon mean feed. They can also learn that being chased somewhere usually leads to increased fear and distress. Cattle are more distressed by being sorted out to go single file up a chute with people hollering at them than they are by the vaccination they get while in the chute. It is extremely important that we make cattle’s first experience with handling or new environments as stress-free as possible so they are willing to do it again and even easier the next time.
It is extremely important that we make cattle’s first experience with handling or new environments as stress-free as possible so they are willing to do it again and even easier the next time.
Arrowquip’s Q-Power 106 Series Hydraulic Squeeze Crush is engineered for quietness to keep animals calm and moving through the cattle handling system.
Facilities—What’s important?
Two things are really important with facilities. No. 1 is that you have some! You need a large pen to gather cattle off pasture, a crowd pen to be able to pressure a small number of animals, a single file alley at least two animals long with some type of head catch at the end and, ideally, a couple of pens to sort into coming out of the chute. The other critical ingredient is that you walk in the facilities to see what’s wrong when animals are balking. Is there a shadow that looks like a bar, or a wet spot on the floor, or is the corner too sharp, is the single file chute a dark tunnel, etc. Facilities don’t have to be fancy, curved, solid–sided, etc., but they should be an aid to your working cattle and not a hindrance.
Facilities don’t have to be fancy, curved, solid–sided, etc., but they should be an aid to your working cattle and not a hindrance.
Cattle handling skills
Simple engineering, like the no-back bar on EasyFlow race sections, keep cattle moving forward through the system.
The secret to asking cattle to move instead of forcing them is understanding the flight zone and point of balance concepts. Cattle, like people, have their personal space. When someone, especially if that someone is scary (remember, our round, close-set eyes tell cattle we are predators) gets too close, we want to move away. It was our decision, and if the scary person doesn’t follow, we don’t feel any stress. The same is true with cattle. If we get a little too close, just inside their flight zone, they will move away as if we asked them to move. If we try to push too hard, there is a good chance they will try to run back by us. Neither cattle nor people want to be forced, and our/their first reaction is to force back. The diagram below shows both the flight zone and the point of balance.
The secret to asking cattle to move instead of forcing them is understanding the flight zone and point of balance concepts.
Getting close to the flight zone asks an animal to move, and when you get too close, the point of balance determines the direction. As a general rule, if you apply pressure in front of the shoulder, animals go backwards or turn away. Putting pressure behind the shoulder will ask the animal to go forward. It sounds simple and it is, but it takes practice. The only way to be good at low-stress handing is to practice. By taking your time, you can walk animals just about anywhere you want them to go, not because you are faster or stronger, but because you know where to be and what actions to take. The golden rule of low-stress handling is slow and quiet. Less stress for you and the cattle.
This blog was reposted with permission by Michigan State University. To see the original version, please click here.
Upgrading or building a new cattle handling system? Read this first
First and foremost, the main priority should always be safety for both cattle and handlers. If you’re upgrading your current system, start at the back and work your way forward to assess every point of safety.
Whether you’re installing a new cattle handling system or upgrading an aging set up, careful consideration should be taken to ensure that money is spent effectively.
1. Make safety a priority
First and foremost, the main priority should always be safety for both cattle and handlers. If you’re upgrading your current system, start at the back and work your way forward to assess every point of safety. For example:
Do you holding pens have the capacity to accommodate the amount of cattle you tend to work at one time?
How vulnerable are you if an animal decides to turn while moving them into the system?
How easy is it to secure the gate behind cattle in the tub?
Is there any point within the race or crush that an animal’s head or leg could get caught?
Does your crush allow you to access the animal without the risk of breaking your arm?
These are just a few of the things you should be looking at. A quick assessment will provide a clear guide to determine what is and isn’t justifiable for the system upgrade.
2. Consider efficiency
Efficiency benefits are two-fold: Cattle that flow easily through the system will be less stressed, which reduces performance setbacks. Cattle that flow easily through the system will also reduce labour requirements. While there are long-term investment benefits in a new system, it’s important to make the most of your budget to get the most bang for your buck.
The Easy Flow Race can help prevent young stock turning and injuring themselves and anti-backing bars can reduce the time your cows spend in reverse.
For example, you may have your heart set on a new hydraulic crush. If that takes up your budget and means the rest of your system remains inefficient and requires two people to herd cattle one-by-one into it, then you aren’t going to see the benefit of that expense. However, if you were to opt for a quality manual squeeze crush and had cash left over to include a sweep pen and race sections, then your business will quickly yield dividends in terms of safety and time.
If you have a very efficient arrangement and find that your limiting factor is the crush then a hydraulic crush is now a better option. A long day working cattle, maybe on a TB test, will be done and dusted sooner and safer – leaving you more time to get on with the day to day running of your farm. It's also worth considering that the reduced physical demands of a hydraulic crush can allow members of staff who aren't necessarily suited to cattle work to be involved and play an integral role in your farm.
3. Use animal behaviour to your advantage
Speaking of efficiency, understanding and working with animal behaviour will reduce stress to you and your cattle.
Cattle do not like dark spaces, noisy equipment and distractions. Using caulked sheeted siding on races and sweep pens massively reduces the noise that cattle are exposed to in what is already a high stress situation.
By nature, cattle like to return to the direction they came from. Highly innovative equipment like the BudFlow Tub is designed with this behaviour in mind, improving the efficiency and ease of cattle flowing through the system.
4. Think about space requirements
Space can also play a part in determining the layout of a system. Smaller sweep pens can still work well, an 8' radius sweep pen for example can be highly efficient, cattle work more quickly in smaller groups as the operator is placing pressure nearer to the lead animal and so even if a 10' radius won't fit, it still needn't limit your processing ability. Also, consider a double race. Races that run side by side help to draw cattle forward, reduce the distance from the crush to the rear of the race while still maintaining capacity and utilise your space effectively. Even if you space isn't limiting you, a double race can still prove a cost effective and low stress option for cattle handling.
Whether you are building a new system or upgrading different components of your existing system, Wise Agriculture can help you determine the most efficient layout for your available space.
Without question, safety is the most important factor to prioritise for any cattle handling system. From there, consider the monetary benefits from the ability to implement better management practices with minimal stress and time resource.
If you’d like more advice on cattle handling equipment, system designs or low-stress cattle handling techniques, please get in touch.
Seven basics to low-stress cattle handling
Whether cattle are being moved to a new pasture or being worked through a handling system, reducing excess noise will help reduce their stress levels.
This article originally appeared in the January 12 issue of The Scottish Farmer.
“If it works for the cow, it works for the person,” says Edward Wise of Wise Agriculture, dealer for cattle handling equipment manufacturer Arrowquip. Through his experience of farming beef and working on ranches in the United States, Mr Wise says cattle handling systems and techniques need to have the safety of the cattle and their handlers in mind.
Below, Mr Wise outlines seven basics for low-stress cattle handling.
1. Have a game plan
Prior to setting foot into the cattle pen, everyone involved in the project needs to be briefed.
“This should include what type of work will be done on the cattle, what everyone’s responsibilities will be and even which pens you want to gather cattle in,” explains Mr Wise. “Communicate everything and don’t assume that your help knows what you want them to do.”
Part of having a game plan also includes having everything organised before cattle are gathered.
“If you’re delayed in getting your project started or are having to stop mid-way through to get more supplies, it’s just going to cause more stress on your cattle – and your help.”
The Q-Power 106 Series Hydraulic Cattle Crush reduces stress to cattle handlers and their livestock.
2. Assess your cattle handling system
Before bringing cattle through the handling system, have a walk through it to see if there is anything that may slow the work flow.
“Cattle will flow better through the race if they can see that they have someplace to go and can see other cattle ahead of them. Walk through the entire handling system looking for things that may obstruct their view or may be flapping in their line of sight,” explains Mr Wise.
It’s also important to pay attention how equipment engineering will affect the movement of cattle. For example, a race section with sheeted sides will reduce distractions, therefore improving work flow.
“Check that gates and latches are easy to secure because poorly designed equipment will slow down progress and reduce safety,” he adds. “Every time a process has to be repeated because a gate has come open or a calf has turned around, the time effort doubles. Not only can this add stress to your stock, but it adds to your wage bill.”
Height adjustable anti-backing bars in the Easy Flow Cattle Race keep animals moving in the right direction.
3. Stay quiet
Whether cattle are being moved to a new pasture or being worked through a handling system, reducing excess noise will help reduce their stress levels.
“If you go into a pen shouting and flapping your arms around, it’s going to cause cattle to get worked up and be harder to handle,” says Mr Wise. “Making noise is important to letting cattle know you are there and can be used to apply pressure, but it needs to be done so appropriately.”
Cattle handling equipment should also be quiet, keeping cattle calm as they move through the system. Arrowquip’s Q-Catch 86 is renowned as the world’s quietest manual squeeze crush, engineered with nylon bushings and a rubber floor to reduce noise.
The Q-Catch 86 Series manual crush from Arrowquip is world renowned for its quietness, which will help reduce stress on cattle and handlers.
4. Understand flight zones
An animal’s flight zone is the space it requires before feeling the need to move when pressure is applied and will vary from animal to animal based on its temperament.
“Within the flight zone is a point of balance, this can be used to move cattle based on where the handler applies pressure. Typically, it is at the shoulder. So, if an animal is facing you and you walk past the balance point and then enter its flight zone, then it will move forward without the need for additional force,” explains Mr Wise. “Cattle handling systems can be designed to utilise this natural behaviour for more efficient cattle handling.”
5. Work in small groups
To help utilise flight zone pressures, work cattle in smaller groups.
“This will help maintain greater control of the cattle by allowing the entire group to be moved with flight zone pressures, rather than just the cattle at the back,” he says. “Rather than battling on to get cattle at the front of the group to move, you’ll be able to get everything where you want them to go much quicker.”
By only bringing small batches of cattle into the forcing pen at a time, handlers can utilise flight zones to move animals more efficiently. The BudFlow uses natural cattle behaviour to improve flow.
6. Don’t rush
The best way to work cattle efficiently and safely is to slow down. Keeping cattle calm and moving at a steady pace will get the job completed quicker than if things are rushed.
“Adding excessive pressure and noise to speed up an animal’s movements is only going to cause it to stress and panic. This is when accidents happen,” Mr Wise says. “Keeping cattle calm and quiet will get the job done quickly and safely.”
7. Make farm safety a priority
Working with cattle can be extremely dangerous if facilities are not fit for purpose and cattle aren’t handled properly. Priorities must be set on improving safety.
“If the best cow on your farm runs everyone she sees up a fence, then it’s time she went. If your cattle handling system consists of a few panels fastened to a calving gate, then it’s time to make an investment into a safer system,” concludes Mr Wise. “There are certain things that must take precedent to reduce the risk of injury and even death on a cattle farm. Your safety, the safety of those who work for you, and the safety of your cattle must be made a priority.”
The Q-Catch Head Holder features dual action pressure to secure cattle for delicate procedures. Height can be adjusted to suit any size of animal.
Want to learn more about Arrowquip low-stress cattle handling equipment? Contact Us.
Arrowquip Q-Catch 86 Series Manual Squeeze Crush Demonstration
Edward Wise demonstrates the Arrowquip Q-Catch 86 Series Manual Squeeze Crush with a split door vet cage and Q-Catch Head Holder.
Edward Wise demonstrates the Arrowquip Q-Catch 86 Series Manual Squeeze Crush with a split door vet cage and Q-Catch Head Holder.
Why Arrowquip?
Find out why we chose Arrowquip!
In 2014 we took delivery of our first Q Catch. An 8300, with many of the great features we see today on the latest Arrowquip crushes but with far more grease points! It was also bright orange, with the Arrowquip branding removed but retained its 'Q Catch' headboard. This wasn't to sell on, this was for everyday use on the farm, replacing a rudimentary, over centre head yoke design.
We were immediately impressed. The build quality was tremendous, far more suited to handle finishing bulls than it's predecessors. The Q Catch headgate wasn't to readjust (what a game changer!) and the speed at which we could run cattle through was fantastic. When vaccinating and weighing bulls onto the farm we could just about cut out a man and still be quicker, just by swapping out our crush.
We soon set about trying to find another the same for other units, they might have been to handle fewer head but the improved safety was more than enough justification. At this point there wasn't a UK importer, and certainly not a comparable squeeze crush on the market. A quick email fired off to Arrowquip HQ in Canada was noted.
In late 2017, whilst power harrowing the last few acres of winter crop ground, a phone call showing a withheld number from an Australian in Canada (?!) set the ball rolling for a new business venture. Mark Firth, son of the Arrowquip founder, was on the lookout for someone to import Arrowquip cattle handling equipment to the UK and had come across an email from North East England sent a few years previously.
A good look at the information on the latest Arrowquip range, much expanded from the era of our 8300, suggested that this might be a good opportunity. David, my younger brother, had recently come back to the farm and the need for a diverse and sustainable income was more apparent than ever. Mark and Shaun (Arrowquip Head of Sales) paid a visit here in December 2017, their commitment to the UK market was apparent. There still wasn't anything comparable on the market and it only takes so many farming friends to comment on how much they like your crush to make sending a large portion of your savings to a Canadian bank account, up front, for a container load of cattle crushes seem less crazy....
The first order was placed June 2018. The research had been done; every YouTube video watched, every competitors crush rattled, the team in Canada spoken to time and again to ensure nothing was overlooked. By the time the first container arrived that August, all but one was sold unseen. Since then things have gone from strength to strength. With an Arrowquip presence in the UK for support and excellent equipment shipped every time, the learning curve has been steep but smooth.
The main lesson: "It's easier to sell quality products, to like minded people, when you use them yourself."
Our 8300 is still in use daily, still as good as the day we installed her. The modern day equivalent, the Q Catch 8600, is practically maintenance free with just one grease point. The rubber floor is made by Goodyear and provides excellent traction and the powder coat finish ensures that it will still look the part in years to come. Arrowquip do not build their equipment to a cost, it's built to be safe, practical and long lasting. That's why there is a 5 year warranty on Q Catch crushes bought today.